T ransometer
The Transometer™ is the first commercial thermoreflectance-based system to measure the thermal conductivity of thin-films as well as the interface thermal resistance between them. The Transometer system’s novel approach collects experimental data from a test sample and extracts unknown parameters from matched computational models of equivalent structures. It can even determine the thickness of opaque thin film layers. Its fully non-contacting and non-destructive technology helps shorten material design cycle time and avoids costly trial and error when dealing with unknown materials or layers of materials. With the Transomete, you can now explore novel thin-film materials and determine material thermal properties without destroying samples along the way.
The Transometer system utilizes a pulsed laser to heat the surface of a sample under test, a CW laser (of a different wavelength) to probe the heated surface of the sample, and a data acquisition PC to capture the measured signal and analyze the data. The thermoreflectance measurement system is based on the principle that the reflectivity of a material changes linearly with temperature in a small, but quantifiable, way. The probing laser reveals those changes by reflecting the laser energy back from the sample surface to the active area of a fast and highly-sensitive photodetector. Since the reflectivity of the surface affects the amount of reflected irradiation, changes in that reflectivity induce variations in the output signal of the photodetector, which are used to extract unknown properties.
The Transometer N8 system consists of a Measurement Head, a support arm assembly, a sample holder assembly, a data acquisition PC, a System Rack Station, a monitor, a keyboard, and a mouse. The Measurement Head and sample holder assembly install onto the provided support arm assembly. The data acquisition PC installs in the provided System Rack Station.
The Transometer program workflow is divided into three parts:
Load Sample Structure Information – Define the test sample structure materials and known properties and indicate the unknown variables that the system will solve for.
Data Acquisition – The Transometer captures a thermal profile of the test sample using a thermoreflectance-based pump-and-probe method.
Fit Data – The Transometer solves for the test sample’s unknown parameters by iteratively fitting a matching computational solution to the acquired data profile.
Data Analysis | Sample Holder Assemblies | Gallery | Benefits | Applications | Transometer Brochure
T ransometerTM Models
T ransometer N8-200
Non-destructive, thermal material properties testing.
Data Analysis
The Transometer collects experimental data of defined sample structures and derives solutions for their unknown parameters by fitting an equation to the Measurement Head’s acquired data. The user may extract up to two independent unknowns, such as the thermal resistivity between thin-films, the thermal diffusivity of a thin-film, and/or the thickness of opaque film layers.
To increase confidence in a measurement set, the Transometer includes a repeatability assessment that allows the user to take multiple trials in the same location of a test sample. The Transometer also features automated spatial scanning when purchased with the automated translating sample holder, enabling it to acquire data at a number of user-defined locations on the same test sample.
TransoViewer™, included with each Transometer, is a program that analyzes collected data at a personal computer, freeing up the Transometer for constant use and multiplying the number of analysts that can work simultaneously. TransoViewer loads a saved Transometer acquisition file and provides the fitting procedure interface for the user to explore other unknown parameters for the same sample structure.
Sample Holder Assemblies
Transometer sample holders mount to the provided support arm assembly. Customize your Transometer sample holder configuration with the following options:
- Chuck Diameter
- The sample holder is offered with a 4 inch diameter or a 6 inch diameter chuck.
- Heated or Passive Chuck
- The heated sample holder consists of a copper alloy chuck that can be heated up to
100°C (212°F) . The sample holder includes a liquid chiller unit to regulate the heat sink temperature. The sample holder chuck and heat sink temperatures are monitored through the Transometer system’s user interface, and the sample holder assembly automatically shuts off if the heat sink temperature exceeds a safe level. The heated sample holder unit mounts to the manual or automated translation stages of the support arm assembly. - The passive sample holder consists of an aluminum alloy chuck that is mounted to the manual or automated translation stages of the support arm.
- Manual or Automated Movement
- In the manual version, the sample holder mounts to two, manual translation stages on the support arm base plate that are actuated by micrometers. The stages give the sample holder a total travel of
25 mm (0.98 in.) in the X- and Y-directions. - In the automated unit, the sample holder mounts to automated translation stages on the support arm base plate. The motorized translation stages are controlled by the Transometer software and enable Transometer automated spatial scanning in the X- and Y-directions. With automated spatial scanning, the user can define a number of test locations on the same test sample, collecting and extracting data over a range of the test sample's surface. TMX Scientific can customize the travel distance and increment of the stage to suit the user’s needs.
Gallery
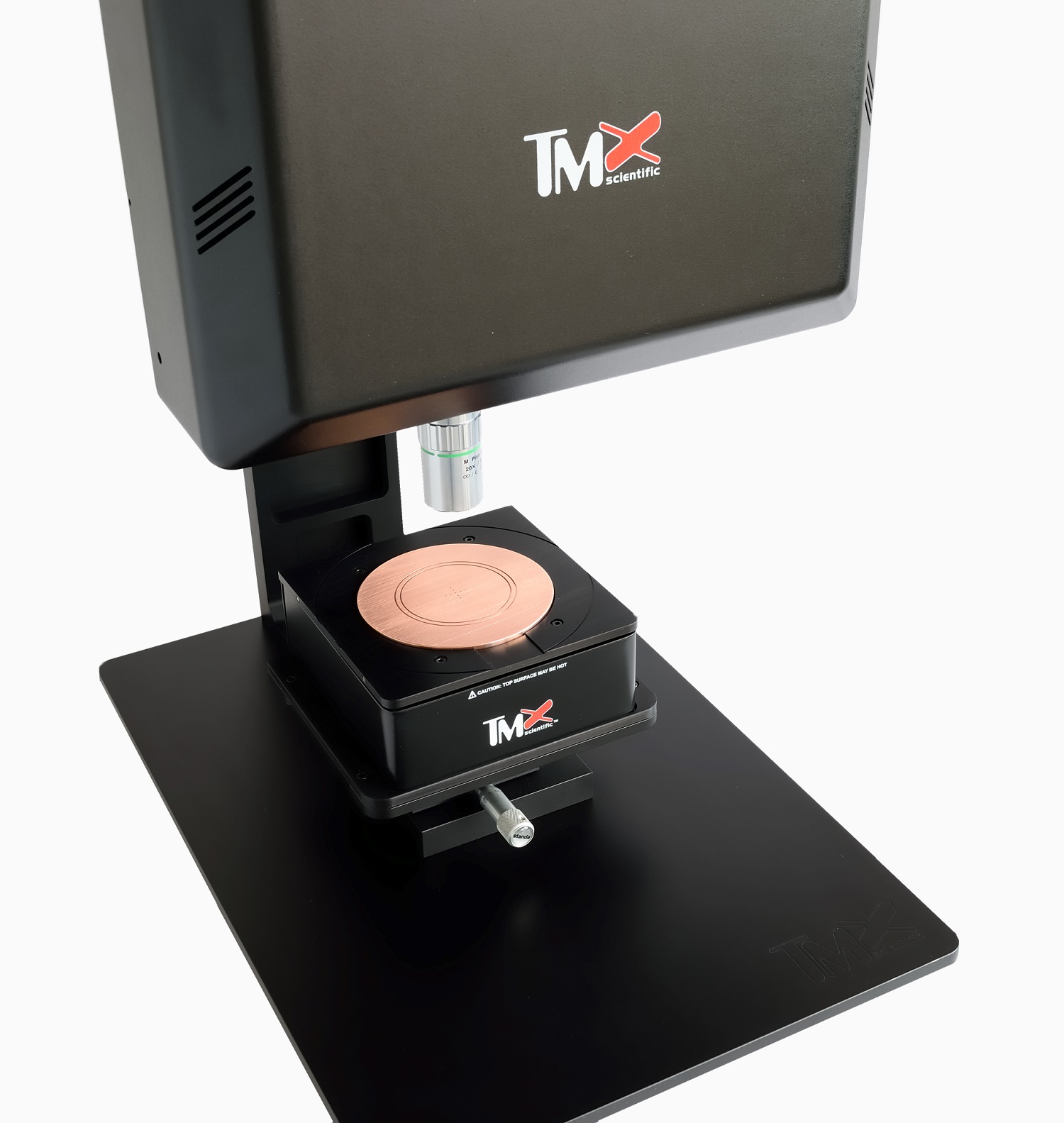
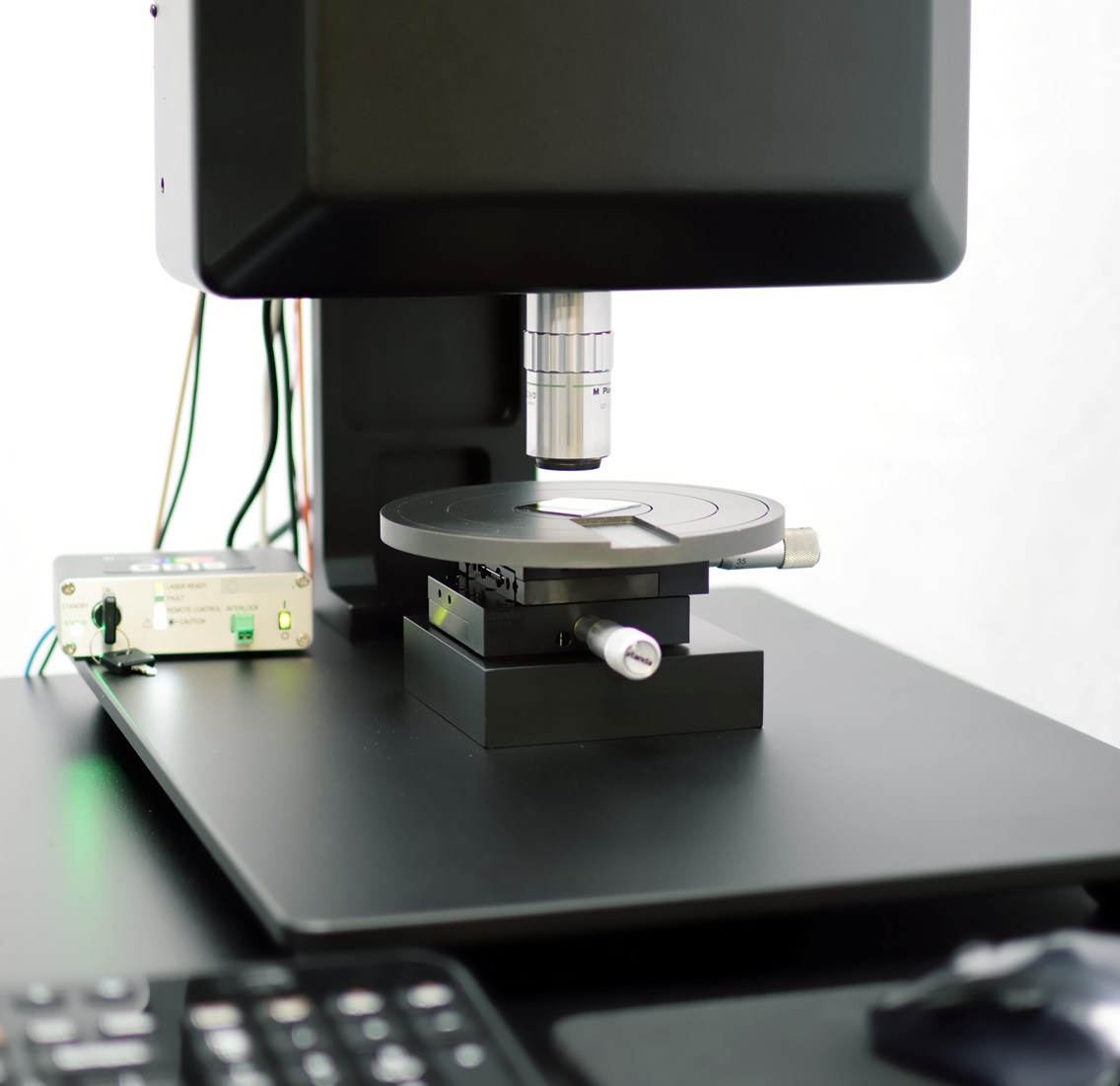
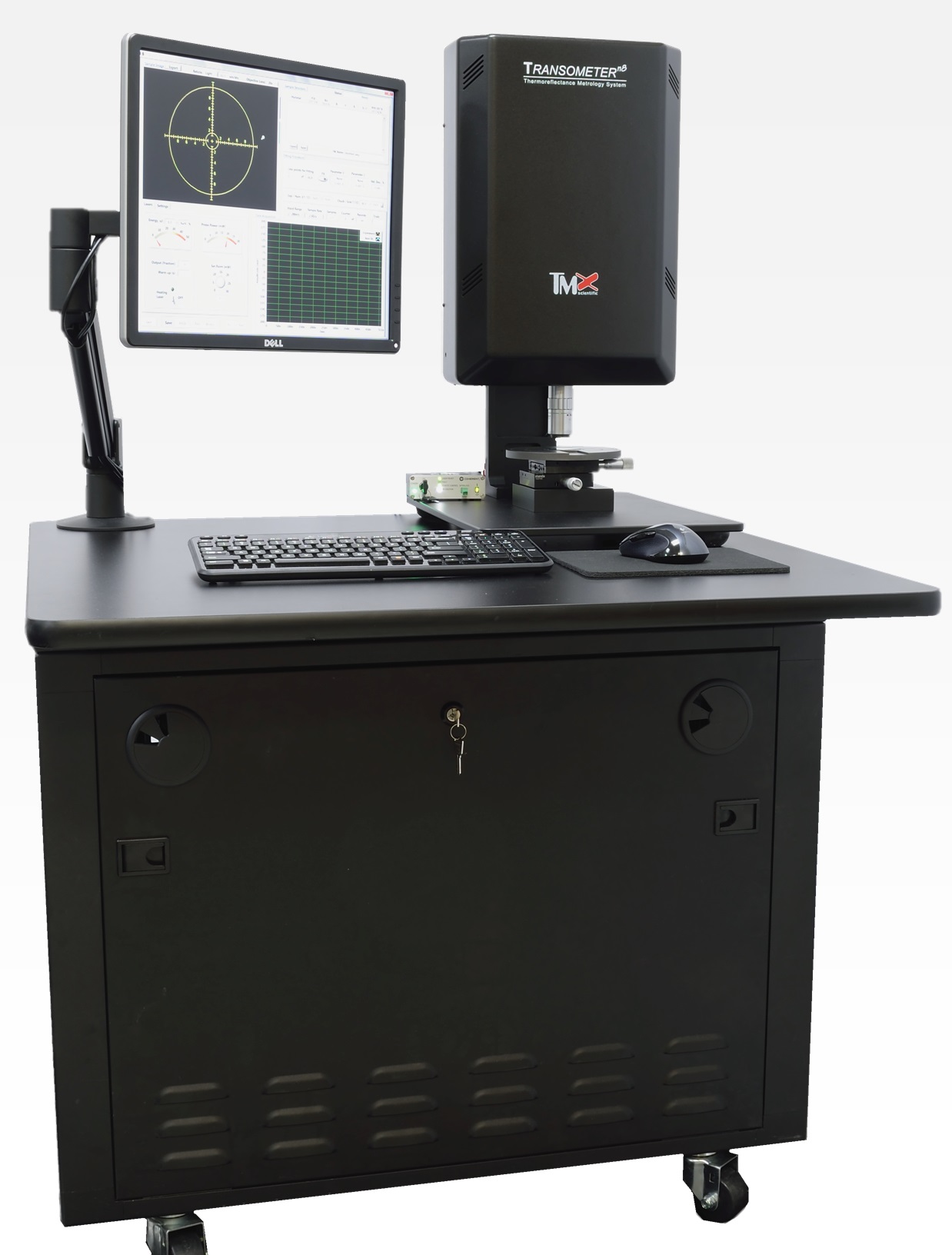
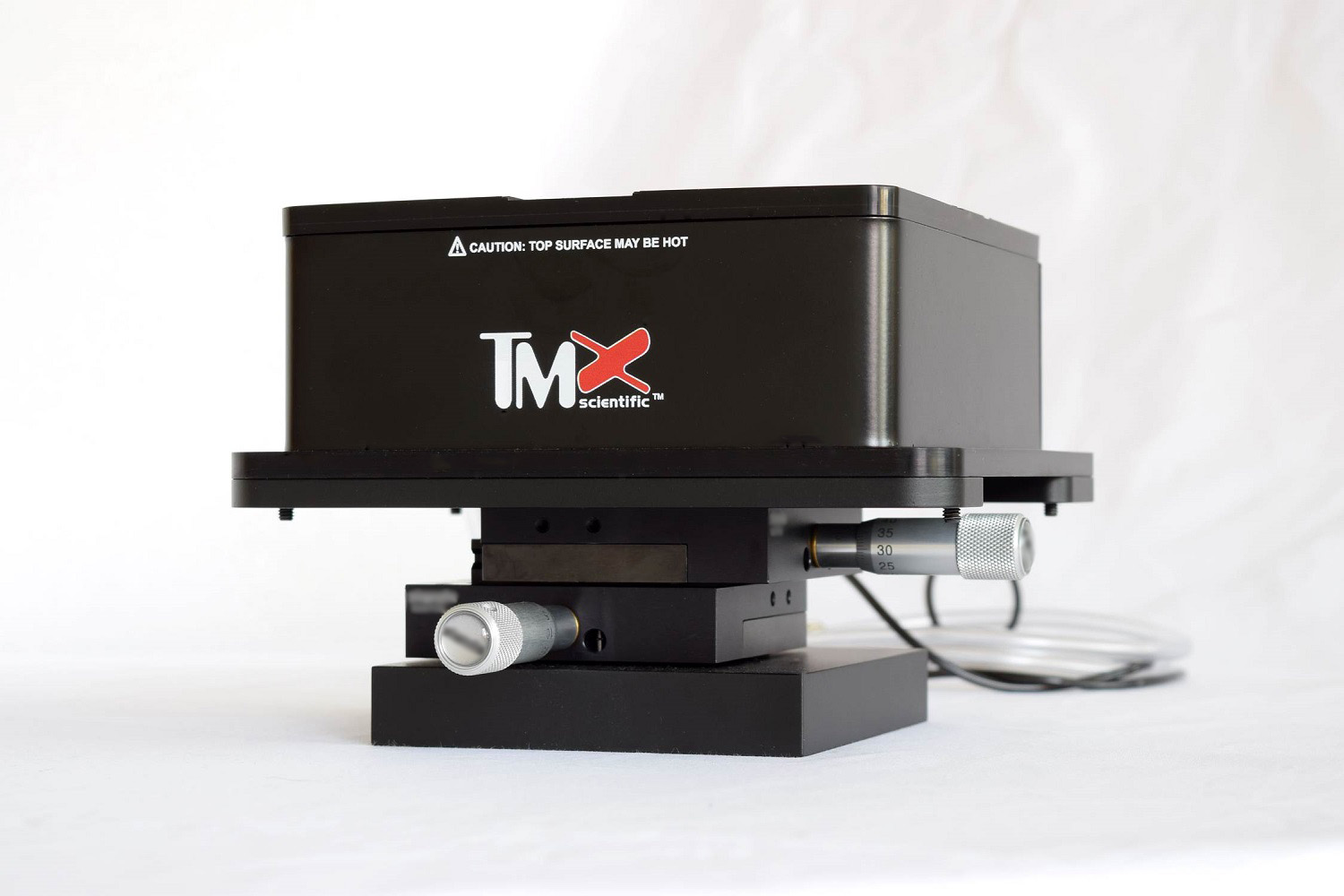
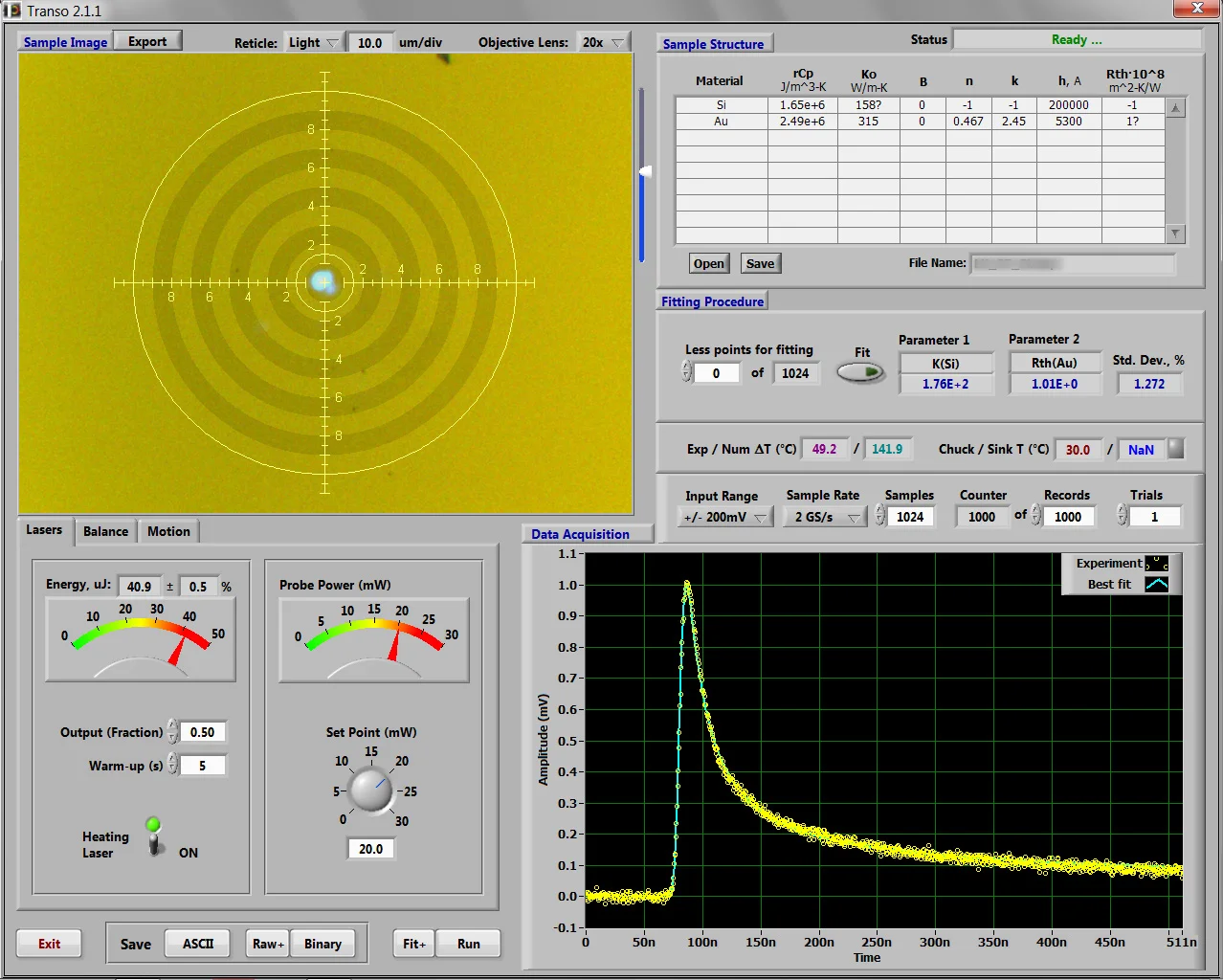
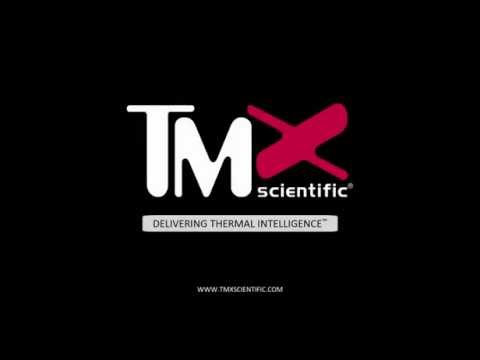
Benefits
- Measures thin-films as small as a few nanometers
- Non-contact and non-invasive, fully optical approach
- Simultaneously measures the thermal conductivity of thin films and the thermal interface resistance between them
- Non-destructive: Minimal sample heating during test
- Ease of use: System is fully computer controlled with an intuitive user interface
- Speed: Single measurement based on hundreds of laser shots takes less than a minute
- Remarkable accuracy: about 2.5%
- Excellent repeatability: within 1%
- Compact and probing station mountable: Lasers are integrated or delivered via fiber optic cables
- Small measurement area: a surface area of 500 microns (0.02 in.) is amply sufficient
- Can also measure the thickness of opaque thin layers
Applications
- Measure thermal conductivity and interface thermal resistance of semiconductors, dielectrics, and metallic thin films
- Measure thermal conductivity of novel bulk materials
- Measure the thickness of opaque thin-films